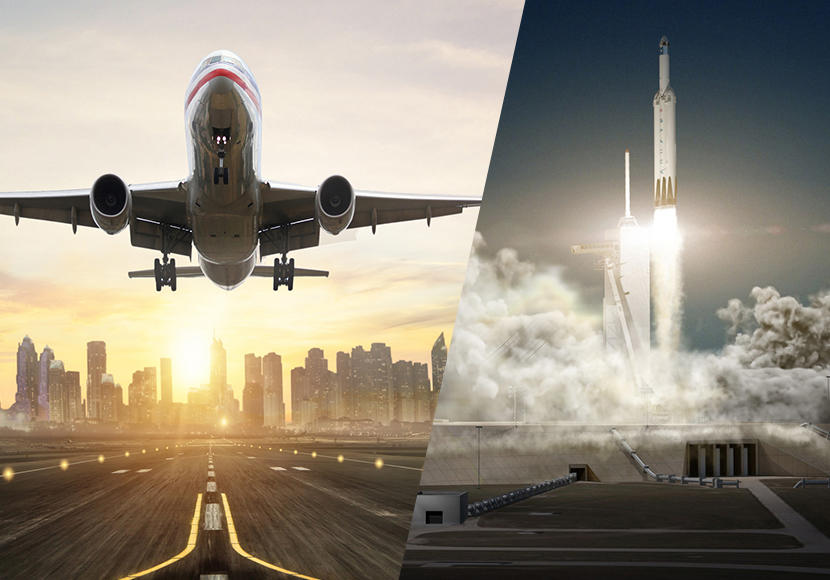
Nowadays the development of aerospace industry needs much more strict demand on the life cycle cost and weight reduction. One of the crucial challenges is making a structure as light as possible without sacrificing its strength. Composites, particularly carbon fiber-reinforced plastic (CFRP), has been used in aircraft designing for years. sandwich structures are the preferable choice for such designs. PMI foam, which is the best suitable structural core material because of its excellent properties, has long been used in the aerospace industry.
Cashem’s high performance PMI foam core Cascell® can meets the requirements from the market. Cascell® WH and Cascell®RS provide optimized cell size for resin absorption and mechanical properties, the correspondent composites can be made through autoclave, RTM or heat molding. It is able to withstand the curing temperature of 180 ℃ and compressions of 0.8Mpa without significant creep. The high-temperature resistance of PMI foam also enables the co-curing with the carbon or glass fiber, which dramatically reduce the production time.